What is the Food Industry’s Manufacturing Process for Flexible Packaging?
5 min read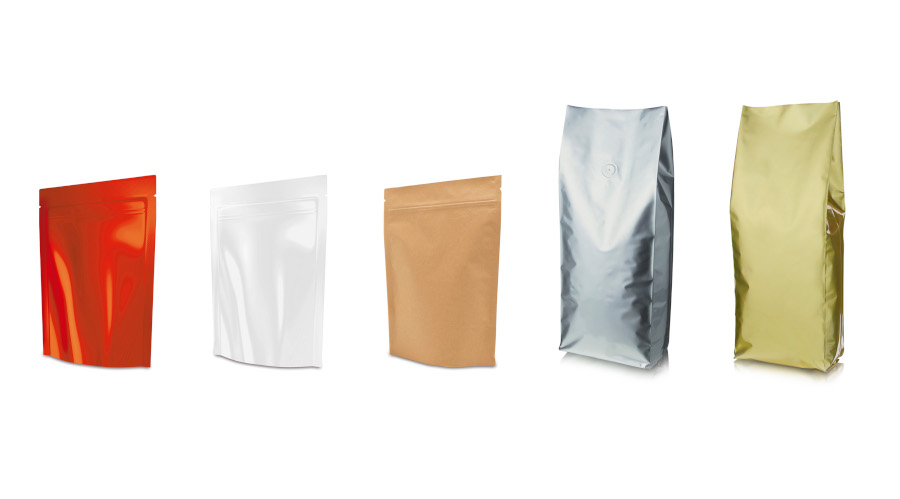
Despite all the major advantages that have been tagged onto it, convenience, adaptability, and cost-effectiveness just to mention a few, flexible packaging is now in the food sector as a main pillar holding it. While they know which film to use, the number one challenge is the actual production of the packaging film. Through the lectures and quizzes, they will look at the materials used, the methods applied, and the products they use in their homes and in the stores that are so easily available because they will focus on various steps.
Flexible Packaging: An Overview
Moldable and flexible packaging materials, such as plastics, or elastic monthly service fees are charged by car leasing companies. This is what the term flexible packaging represents. A lot of packaging categories, like pouches, bags, films, and wrappers fit into this category whereby they are commonly used in the food industry. First of all, it is a hassle-free and easy-to-handle option available on the market and secondly, it can maintain product freshness therefore it is the most preferred packaging type
Components of Flexible Packaging Surface Animation Display A variety of surfaces may be animated through lighting techniques, shadows, and other visual effects to showcase the characteristics and benefits of different raw materials used in manufacturing flexible packaging.
The collection and distribution of raw materials marks the commencement of the manufacturing process. The fact that it has barrier characteristics superior to that of aluminum foil is what is mostly utilized as a cover that does not allow moisture, light, and oxygen to pass through. This is because being easy to decay and pro-environment, paper is often used.
Extrusion of Films
The extrusion of film comes next, following the procurement of raw ingredients. The materials for many different kinds of flexible packaging are made from thin films, which are produced by melting plastic resins. Although there are other methods for extrusion, the most often used ones are blown film and cast film extrusion.
The process of blowing plastic through a circular die creates a tube when the material melts. The tube expands to the required thickness when air is blasted into it. The outcome is a big roll of plastic film when the enlarged tube is cooled and flattened. Alternatively, melted plastic is extruded onto a cooled roller in cast film extrusion, which yields a flat sheet of film. Based on the application, each approach has different benefits.
Covering and Shielding
In the production process, lamination and coating come next after film extrusion. To produce a composite construction with improved qualities, laminating entails gluing many layers of material. Aluminum foil, paper, and plastic, for instance, can be combined to provide strength, barrier qualities, and aesthetic appeal in a typical laminated construction.
Adding protective layers or unique qualities to flexible packaging may also be achieved by coating. Abrasion, UV radiation, and moisture-resistant coatings are a few examples of what this might comprise. Whether it’s maintaining the crunch of snacks or the freshness of coffee, lamination, and coating are essential components of packaging designed to specifically fulfill the demands of food products.
Personalization and Printing
The materials for flexible packaging may now be printed on and customized after they are produced. A flexible packaging material manufacturer can embellish the package at this stage with logos, product details, and other imagery. Although flexography and rotogravure are the most often utilized printing processes, flexible packaging may employ other techniques as well.
Instead of using engraved cylinders for rotogravure, flexography employs flexible printing plates to transmit ink onto the packaging material. Superior printing with vivid colors and accurate detail is provided by both techniques. Resealable features, rip notches, or unique forms for the package are examples of customization choices available at this point.
Consolidation of Bags and Pouches
The box must then be formed into its final shape when the printing and personalization are finished. Making bags, pouches, or other flexible containers out of the flat film is the process here. The process for accomplishing this might vary according to the kind of packaging that is being made.
To construct the structure of a pouch, the film is cut and sealed at the edges. Depending on the design and material, the sealing process can be carried out using ultrasonic, pressure, or heat. Additions like handles, spouts, or zip-lock capabilities may be necessary for bags. To meet the unique needs of the food product, a practical and user-friendly packaging solution must be developed.
Testing and Quality Assurance
To guarantee that the flexible packaging satisfies industry standards and regulations, quality monitoring and testing are crucial throughout the production process. To do this, tests for strength and durability as well as flaws and barrier characteristics verification are carried out. Food goods are shielded from contamination and damage by quality control techniques, which assist in guaranteeing that the packaging will function as planned.
The ability of the packaging to maintain food over time may also be tested by manufacturers through shelf-life studies. For products like canned foods or packaged snacks that have extended shelf life, this is especially crucial.
Sales Via the Internet and Distribution
Distributed to food manufacturers and merchants for use in packaging food goods, the flexible packaging is made and then packaged. Food firms may now easily purchase and personalize packaging for their products thanks to the abundance of manufacturers that are offering food packaging containers online as a result of the growth of e-commerce.
Owing to its accessibility and ease, flexible packaging sales online have become more and more common. To ensure they acquire the ideal packaging for their products, food firms may select from a range of packaging types, sizes, and designs.
Conclusion
Food sector manufacturers use a multi-stage, intricate procedure to create flexible packaging. To create packaging that satisfies the expectations of the contemporary food business, every stage from sourcing raw materials to extrusion, lamination, printing, and customization is vital. Although internet sales provide food firms more freedom in obtaining the necessary packaging, quality control, and testing guarantee the finished goods are safe and effective. Innovative solutions that are provided by flexible packaging are always evolving and help the food business succeed.